Cómo funciona la primera planta que produce celdas y baterías de litio en Argentina
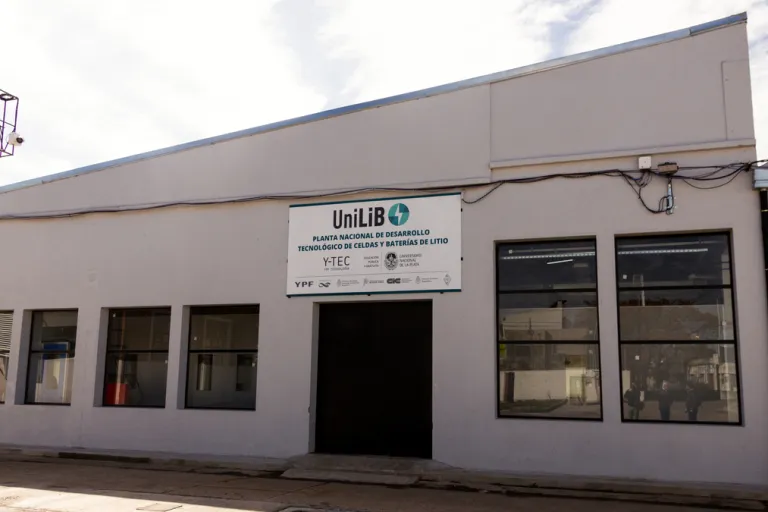


A partir de las amplias reservas del mineral en el país, una fábrica de celdas de litio está próxima a comenzar su producción en La Plata. El desafío de llegar a la industrialización y el paso a paso de un novedoso proceso industrial.
Por Lucas Martínez
Con el 12% de las reservas globales del popular “oro blanco”, el NOA se estableció en tiempos recientes como una concreta oportunidad para desarrollar este mineral. El recurso se obtiene principalmente en las 870.000 hectáreas de los salares ubicados en las provincias de Jujuy, Catamarca, Salta y La Rioja, donde se calcula la existencia de unas 22 millones de toneladas de litio.
El litio de más fácil extracción y mejor calidad se encuentra depositado en las salmueras debajo de la superficie de los salares. Esas salmueras se extraen con perforaciones no mayores a 200 metros y luego se dejan reposar en piletones entre 18 y 24 meses, para que se evapore el agua y se concentre el mineral.
En la Argentina, el litio se vende como commodity al que solo se le realiza este tratamiento básico in situ, que es llevado adelante por las mineras extranjeras para transformarlo en carbonato de litio y así exportarlo.
En ese escenario aparece una iniciativa platense que está muy cerca de comenzar su producción. Se trata de UniLiB, la primera planta industrial en Latinoamérica que fabricará celdas de litio, un proyecto que lleva muchos años de trabajo en conjunto entre la Universidad Nacional de La Plata (UNLP), Y-TEC, la empresa de tecnología de YPF y el Conicet, con el apoyo del Ministerio de Ciencia, Tecnología e Innovación.
La celda constituye la unidad más pequeña y crítica de una batería, que se compone a grandes rasgos de dos polos (cátodo y ánodo), separados por una sustancia conductora (electrolito) y unidos por un circuito externo. Las celdas son utilizadas como bien intermedio del proceso de ensamblado: varias conforman un módulo de baterías que a su vez constituyen packs.
Por ser el litio uno de los métodos más eficientes para conservar la energía, el uso de las baterías de este tipo no para de crecer a nivel global: van desde almacenamiento de otras energías (solar, eólica, etc.) hasta el abastecimiento de las baterías para celulares, vehículos y todo tipo de aparatos.
Su valor, además, crece significativamente a medida que avanza en su industrialización. El objetivo es abastecer a la industria actual –de vehículos eléctricos y celdas para usos domiciliarios- y generar un conocimiento que permita crecer en el sector privado.
La instalación demandó una inversión total de 7 millones de dólares y su puesta en marcha está pautada para antes de fin de año, aunque las primeras entregas aún no tienen fecha confirmada. Tendrá una capacidad de producción anual -medida en energía almacenada- de 13 MWh, equivalente a 1.000 baterías para almacenamiento estacionario de energías renovables o unas 50 para colectivos eléctricos.
La capacidad de la planta será de 300 celdas por día y la operación para fabricarlas demandará 20 empleados por turnos, aunque en principio la instalación solo trabajará con un turno. Las primeras celdas estarán destinadas al abastecimiento de proyectos públicos, como el desarrollo de colectivos eléctricos, proyectos de energía fotovoltaicas.
También hay interés del Ministerio de Defensa en emplearlas para sus radares, y hubo acercamientos de la automotriz Coradir para el modelo TITO, el único vehículo 100% eléctrico que se produce en el país.
Según le informaron a Dinamicarg integrantes de la coordinación de esta iniciativa, Y-TEC y UNLP están apadrinando la construcción de otra planta seis veces más grande en Santiago del Estero, luego de que el gobernador provincial visitara hace unos meses la planta platense.
Actualmente, la nueva fábrica se encuentra en el proceso de compra de los equipos y debería ponerse en funcionamiento en la segunda mitad del 2024.
Cabe señalar que junto al desarrollo de la planta se planificó la formación de recursos humanos y la producción de conocimiento como otro de los objetivos centrales. “Se armó una capacitación entre la UNLP e Y-TEC para operarios de planta manufacturera, y luego se diseñó y dictó en la Escuela de Oficios de la Universidad el primer curso de capacitación para operarios de planta de fabricación de celdas de Litio de Argentina” indicó Javier Díaz, secretario de Vinculación e Innovación Tecnológica de UNLP.
Así se fabrican las celdas de litio
Para conocer con mayor profundidad los detalles de la operación, Dinamicarg tuvo la posibilidad de realizar una visita a las instalaciones con la guía de Javier Díaz, secretario de Vinculación e Innovación Tecnológica por parte de la institución académica y el Ingeniero Juan Aiub de Y-TEC.
Según explicaron los especialistas, la planta ya cuenta con todos los equipos instalados registrando un avance del 90%. Allí, se producirán celdas de Ion Litio, la unidad mínima de almacenamiento de energía que componen las baterías, “varias celdas en simultáneo y en paralelo le dan forma a una batería”, detalló Aiub.
Una celda incluye dos tipos de electrodo, el ánodo que es por donde se lleva a cabo la oxidación, y el cátodo donde realiza la reducción. El primer paso del proceso industrial consta en preparar y pintar los electrodos con los materiales activos.
“El cátodo va a estar pintado con la materia prima en base de litio y el ánodo con grafito”, señaló el ingeniero. “La primera etapa es preparar las pinturas, los sólidos van a estar en suspensión en un solvente que puede ser orgánico o agua”, continuó.
En esta instancia la planta está dividida en dos, ya que ese proceso trabaja con los dos tipos de electrodos en paralelo. Las habitaciones donde las mezcladoras que pintan los cátodos y electrodos deben tener una pureza de aire elevada y muy poco contenido de humedad, por eso los paneles empleados en las divisiones es de un tipo especial utilizado en el sector farmacéutico.
“Una vez preparada la pintura en la mezcladora, el siguiente paso es pintar un rollo continuo que tiene entre 200 y 400 metros de aluminio y de cobre”, remarcaron los especialistas.
Este proceso se realiza dos veces, primero se pinta una de las caras del rollo y se pasa por unos hornos que se dividen en dos filas, una para cada electrodo, donde se seca la pintura a una temperatura que oscila entre los 40° y 70°. Posteriormente el proceso se repite con la otra cara.
Una vez impreso se evalúa el grosor del papel que debe tener cerca de 40 micrones de pintura de cada lado. El siguiente paso es comprimir las planchas para llegar a los 20 micrones para lograr una mayor densidad energética y garantizar la continuidad molecular.
La siguiente etapa consiste en el cortado del rollo ya pintado, secado y comprimido. Mediante una maquinaria especial “que saca segmentos y pasamos de un papel continúo enrollado a un saca bocados que lo divide en unidades”.
Estas unidades se asemejan a pequeñas planchas de papel que van a conformar la celda. En total, cada celda se compone de 18 ánodos y 18 cátodos.
Luego todas las unidades de papel segmentado se enhebran para formar la celda. Luego se elabora la bolsa que va a contener la batería y que tiene un doble recubrimiento de polímero que tiene un mayor grosor y un excedente donde se acumulan gases.
“En la siguiente sala se va a realizar un proceso manual una vez tengamos el sobre y el paquete de electrodos y vamos a constituir la batería y vamos a sellar una de las caras, dejando abierta la otra”, explicó Aiub. Luego se deja secar por varias horas ya que la humedad afecta directamente la eficiencia del almacenamiento energético.
“Después vamos a tomar el paquete y le vamos a agregar 20 mililitros de electrolitos que lleva cada una de las celdas para elevar la transferencia de electrones y vamos a cerrar la otra cara formando el pouch propiamente dicho”, continuó. Desde ahí, la siguiente etapa consiste en comprimir y dar forma al pack definitivo aún sin remover el excedente donde se siguen acumulando los gases.
Finalmente, en una línea de vacío se pincha la bolsa para que salga el excedente y en la última maquina se corta esa sección y la celda queda lista. El último proceso consta de ubicar la batería en cargadores y descargadores donde se la somete a 20 ciclos para verificar y clasificarla en base a su calidad.
Fuente: Dinamicarg.com